Despite COVID-19 (or, in part, because of it), the residential construction sector is performing well. Housing demand continues to remain strong while supply is limited in most areas. Home builder confidence – as measured by the NAHB/Wells Fargo Housing Market Index (HMI) – increased in August to a level of 78… matching an all-time high in the index’s 35-year history.
However, the crisis is adversely impacting material costs, an effect that is expected to linger. Consider the recent surge in lumber prices, which have increased by more than 110 percent since mid-April. And added an estimated $16,000 to the cost of a new home. In addition, builders are experiencing delays in getting other critical materials such as oriented strand board (OSB) and wallboard.
The pandemic has also created increased concerns surrounding architecture and development… including sustainable building practices, affordable housing, climate change and rising seas.
Following are three housing trends gaining traction during COVID-19… and likely to continue into the future.
Going Modular
While prefab construction has been on the rise for several years, it has been gaining momentum in the wake of advances in technology and a shifting economic environment.
Projected growth for prefab and modular homes has shown steady growth during the past few years, and this upward trend is expected to continue beyond 2020. In fact, the prefabricated building market is projected to grow at a compound annual growth rate (CAGR) of more than eight percent from 2019 to 2025.
Prefab and modular construction offer the convenience of having a mostly-built home delivered to a site. Because the homes are built in a factory and then finalized at the build site, they can be constructed in a much shorter time.
In fact, according to a 2019 report from McKinsey & Co., recent modular projects have accelerated project timelines by 20 to 50 percent. The report also noted that the construction method can decrease project costs by as much as 20 percent.
Prefab homes are energy-efficient and reduce construction waste. Factories typically order construction materials in bulk. Whatever isn’t used for a particular project remains in inventory rather than ending up in the landfill… as happens on most site-build projects.
In addition, prefab and modular homes are typically built using computer aided technology to exacting specifications and constructed to ensure they can withstand transport to the final site. As a result, these homes can be stronger and more resistant to structural damage. And, since they are built in a controlled environment with highly detailed plans, few delays are encountered – resulting in shorter timelines.
Another significant advantage revolves around workforce challenges. In remote or rural areas – where the construction workforce may be limited – building homes in a factory and then transporting them to a jobsite can be more cost-effective. Similarly, projects in urban areas typically have higher labor costs. As such, modular construction has the potential to reduce those costs.
Moreover, in an age when social distancing is so important, modular construction can help home projects move forward with less contact between individuals – an important advantage.
Modular housing also lends itself to creative housing solutions – something that is increasingly top of mind when it comes to affordable housing challenges. Module, a housing startup based in Pittsburgh, is in the process of building unique, two-story homes that can easily be expanded to accommodate a growing family. The units begin as small as 500 square feet, which makes the initial cost of ownership very reasonable. When a family requires additional space, the home’s roof can be removed and another unit can be added on top to create a third floor.
Adding Dimension
Some companies are taking the affordable housing concept even further. Austin-based Icon is using 3D printing technology to quickly build a home. The company’s printers are shipped to the homesite and then the home is built using a device that requires the presence of just a few crew members. The process is fully automated, including the mixing and pumping of the proprietary concrete used to build the home.
Icon built the first permitted 3D-printed home in Austin. The 350-square-foot home was printed by a device called the Vulcan I in approximately 48 hours. The cost for the printed portion of the home (the roof was not 3D printed) came in around $10,000… an amount well below the average cost for a home of similar size and quality.
This approach to housing is catching on: the company recently announced that it had secured $35 million in venture capital funding. The funds will be used to move Icon’s 3D printing technology out of the R&D stage and into a mainstream offering that will allow other companies to print the homes. Icon’s homes could potentially be for sale in Texas as early as 2021.
A Sea Change
Concerns over climate change and rising sea levels are also top of mind these days. The increasing intensity of hurricanes along with eroding coastlines are causing a re-evaluation of building codes and construction approaches. Most recently, Hurricane Laura, which hit the Louisiana coast, demonstrated the importance of this issue for coastal cities bordering the Gulf of Mexico and the Atlantic, in particular.
Instead of constructing more robust seawalls to preserve these cities, some people have been wondering, “Why not move out onto the sea itself?” It’s by no means a new idea, as people have been living on water for centuries.
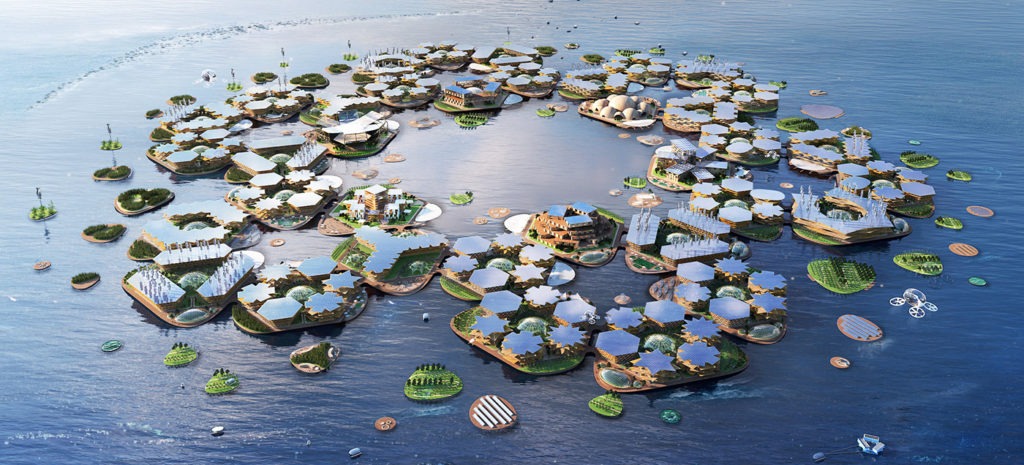
French Polynesian politician turned entrepreneur Marc Collins Chen certainly thinks it’s a workable solution… and a key to the future of housing. Chen founded a company Oceanix, which partnered with Danish Architecture firm Bjarke Ingels Group to create Oceanix City, a self-contained, modular city that was unveiled for the United Nations Habitat Program in 2019.
A concept at this point, Oceanix City would consist of a series of 4.5-acre floating platforms made of wood and bamboo. Each anchored platform would house 300 people. Markets, farms, low-rise apartments and solar panels would stack atop the platforms. Cages under the city could harvest scallops, kelp, or other forms of seafood. The city would grow in a fractal pattern: Six linked platforms, like a hexagon of a honeycomb, would become a village. Six of those villages would be a 10,000-strong town covering 185 acres.
Oceanix envisions a completely closed loop system. All food for residents would be grown on the man-made islands. All water would be captured there. All waste would be repurposed, and all of these fundamental operations would use only energy that could be harvested or generated by the floating city itself.
Unlike “seasteading,” Silicon Valley’s vision of independent city-states that float outside national borders and boundaries… the islands proposed by Oceanix would follow local laws. Chen said he was “not ready to share” projected costs – but said construction costs would stay low – because the floating hexagons can be mass-produced in factories and towed to destination bays.
To eyes grown weary from pandemic lockdowns and disruption, what stands out about Chen’s concept is how easy it would be to distance and quarantine in a modular city. While this particular floating city concept addresses everything from energy independence to locally sourced food, from zero emissions to self-contained water systems, it also allows for contagion mitigation. Communicable disease is probably not something the team responsible for this concept spent much time thinking about, but their idea is even more appealing today given what the world’s most pressing crisis is in the summer of 2020.
While floating cities may seem far off, they might be closer than they seem, as city planners look for alternative housing options in coastal areas.
The pandemic has made us rethink many areas of our lives. After the crisis passes, architects, builders and engineers will continue to look for interesting ways to accommodate a changing housing landscape. Will housing ultimately be reinvented? The only thing constant of course, is change.